Codigo Escuela 4.0
3D printing is a manufacturing technique in which material is deposited or added, hence the technical name "Additive Manufacturing". Its opposite is "Subtractive Manufacturing", which is based on removing material using machines such as lathes and milling machines. 3D printing also falls under "Digital Manufacturing", which is the manufacturing of physical objects using computer-controlled tools. Digital manufacturing requires a CAD model of the part to be manufactured and a CNC machine.
History
The origin of 3D printing dates back to the 1980s when Dr. Kodama at the Nagoya Municipal Institute of Industrial Research devised a technique for manufacturing an object layer by layer. Eventually the founder of 3D Systems, Chuck Hull, filed the first commercial patent in 1984 for a technique called "stereolithography", now called SLA. This technique involves making an object layer by layer by curing a photo-curable resin using a directed beam of light.
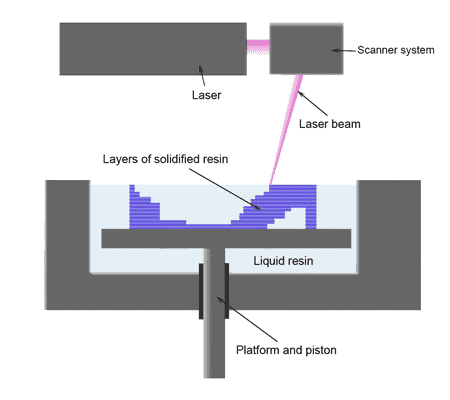
Stereolithography (SLA)
Two years later, Professor Carl Deckard of the University of Texas filed a patent for Selective Laser Sintering or SLS, which fuses a plastic powder with the help of a laser to form the different layers of the part. At the same time Scott Crump, founder of the Stratasys group, developed one of the first fused filament 3D printer. This technique was called FDM and is currently the most widely used technique worldwide.
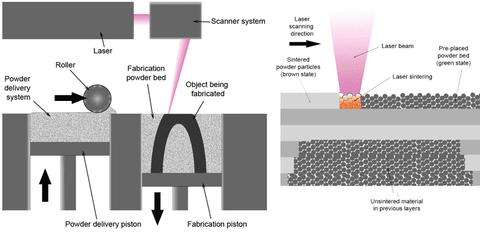
Selective Laser Sintering (SLS)
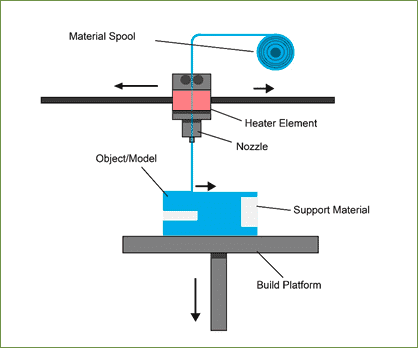
Fused Deposit Modelling (FDM)
Additive manufacturing continued to grow and since the 1990s new manufacturing techniques have appeared, such as binder injection moulding and PolyJet. In the 2000s the latest in additive manufacturing appeared: 3D printing of metal parts, which would be a modification of the already known SLS but replacing plastic with metal and electron beam melting, which is very similar to the previous one but replaces the laser with a beam of electrons, thereby melting the metal in a more controlled way.
FDM vs FFF
As previously mentioned, this type of additive manufacturing technology deposits a thermoplastic material layer by layer to manufacture an object. This work is mainly based on this technology as it is the simplest and therefore the most widespread worldwide.
There are several types of machines within this technology, the fundamental difference between them is the coordinate system they use. We can classify them as follows:
Cartesian
The most widely used coordinate system in the market. It use 3 orthogonal axes for movement.
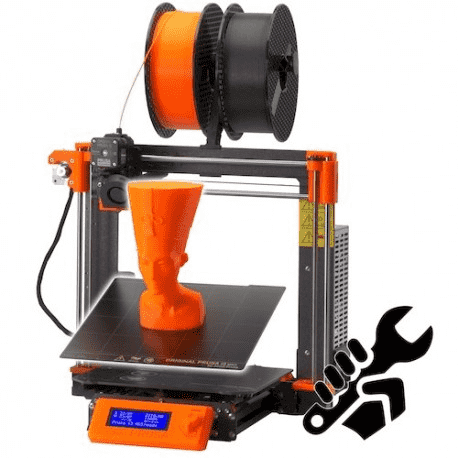
Cartesian 3D Printer MKS3 by Prusa
Delta
A Delta printer relies on cylindrical coordinates for its motion, requiring at least two motors to be synched up to produce a straight line. The part being built is static throughout the manufacturing process.
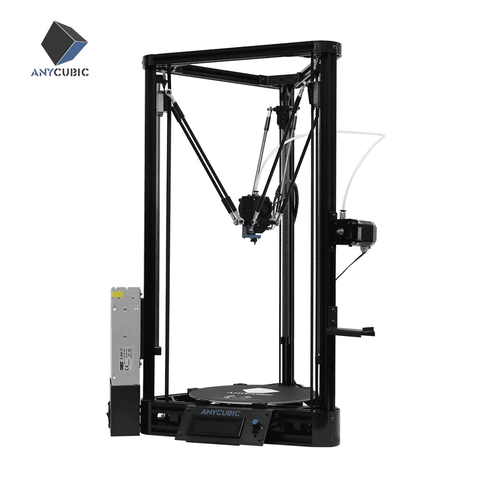
Delta 3D printer by Anycubic
Polar
Polars, as the name suggests, use polar coordinates for positioning. The difference with respect to delta printers is that the part is able to rotate on its vertical axis.
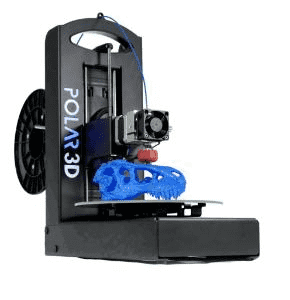
Polar 3D Printer by Polar 3D
Robotic arms
Robotic arms, at the end of which the head is mounted and can therefore have several degrees of freedom.
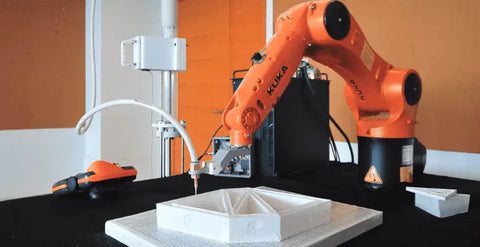
Robotic arm 3d printer
Hybrid 3d printers
Hybrid printers, capable of accommodating different printheads for both additive and subtractive manufacturing. These machines would fall outside this fundamental classification as their coordinate system can be any of the above.
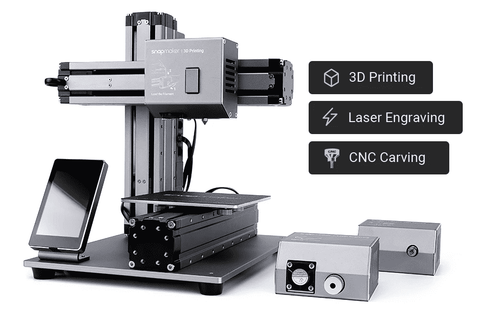
Hybrid 3d printer by Snapmaker
Within this classification there is an infinite number of 3D printers with different characteristics and capacities.
Another classification would be according to the extrusion system, which could be bowden or direct. The bowden system has the extruder and the hotend separated by a PTFE tube; while in the direct system both parts are joined and the PTFE tube is not necessary.
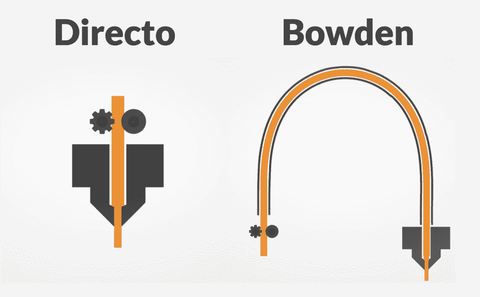
Extrusion system of 3D printing
Both extrusion systems can have the ability to print with one or more materials at the same time, this is called multi-extrusion. There are two types, those that share the same hotend and those that have different extruders, one for each material.
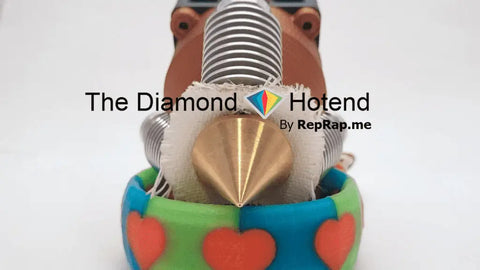
Diamond Hotend by RepRap
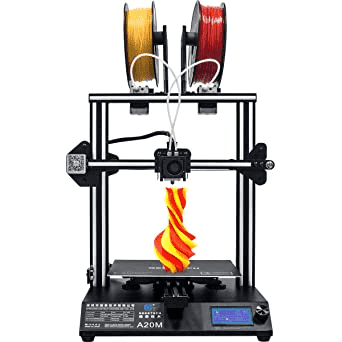
Double extrusion by Geetech
Among those that share hotend we can find the multiextrusion proposed by the manufacturer Prusa3d, which has a material selector and a single hotend. This system slows down the printing process a lot, as well as adding an extra complication when it comes to calibration, as a very meticulous calibration is necessary for it to work correctly.
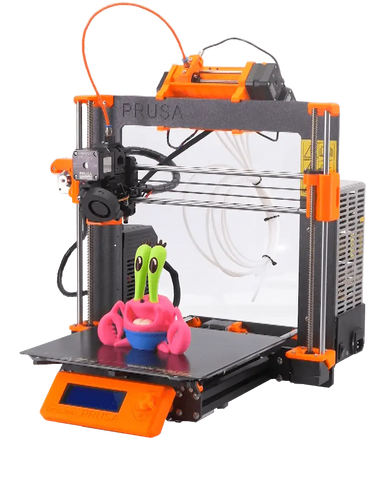
MMU 2.0 by Prusa
In turn, within the independent multiextrusion, we can find a system called IDEX. This has the particularity that its extruders move independently on one axis, normally the X axis, achieving greater precision and greater capacity to combine different materials. In addition, it has the capacity to duplicate the constructed part in the same print due to the independence of both extruders.
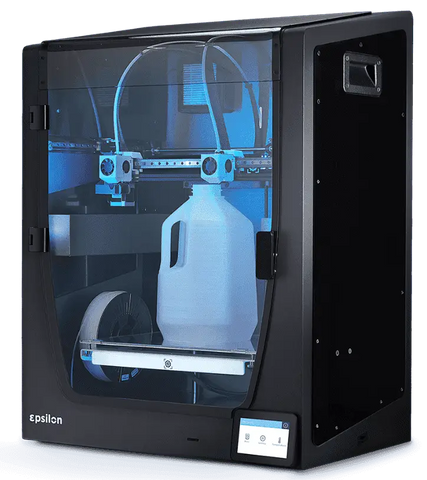
IDEX 3D printer (Epsilon) by BCN3D
To finish with multi-extrusion, it is worth mentioning that last year the British manufacturer e3d launched the so-called "toolchanger", a 3D printer that is capable of automatically changing its head as if it were an industrial CNC machining system, allowing different materials to be printed and even changing printing parameters.
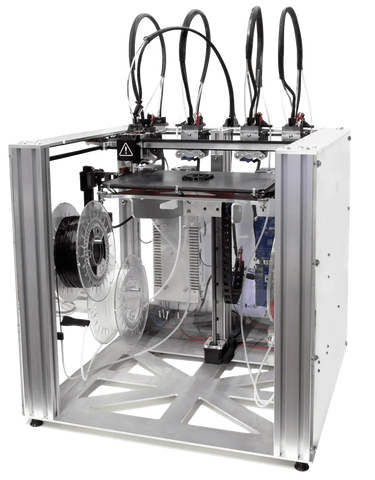
Toolchanger by e3d